Solar PV manufacturers have been highly effective at driving down manufacturing costs over the past decade. However, the era of “easy wins” has ended. Gains will now be harder fought, likely relying on either alternative materials or new technologies. This analysis comes from the Solar Costs and Technology Service, which provides a full view of the solar photovoltaic (PV) supply chain, from key raw materials to final modules, analysing changes in technology and manufacturing costs that will define the future for manufacturers, end users and investors.
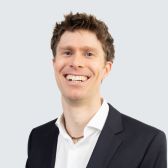
Author Alex Barrows
Head of PV, Exawatt View profile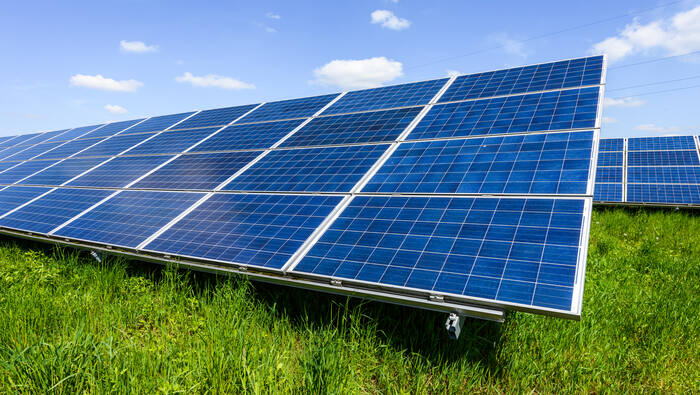
PV modules: Moving from an era of cost-reduction to a time of hard-fought performance improvement
Until around 2017, avenues for absolute reductions in PV manufacturing costs (in a cost-per-module or cost-per-m2 sense) were plentiful, while module efficiency improved slowly. More recently, such cost reductions have become harder to realise, with these absolute costs showing little reduction. Largely, this is a testament to the enormous successes already achieved by the industry in optimising processes, reducing materials usage and driving down the costs of key input materials.
Since 2017, module efficiencies have increased rapidly, driven by advances in technology at the wafer, cell and module levels. At Exawatt (now part of CRU Group), we talk about the PV industry having transitioned from its previous “cost-reduction era” to a “performance-improvement era”. The industry’s evolution is now principally driven by improvements in performance at acceptable costs, rather than reductions in absolute cost at acceptable performances.
The Solar Technology and Cost (STAC) Service is based on the combined knowledge of CRU, Exawatt and US-based testing laboratory PV Evolution Labs (PVEL). The data and insight in this service is used by organisations across the value chain. Understanding raw material markets, policy, as well as the performance and reliability of solar technologies are all vital; and understanding the linkages between these factors is necessary to accurately forecast solar supply, demand, cost and price dynamics.
The outlook is for limited manufacturing cost reductions
Materials costs dominate the manufacturing cost structure for leading manufacturers in China and SE Asia, with frames (predominantly made from aluminum but also galvanized steel), glass, backsheets, encapsulation materials and silver paste all being key input costs. Other costs such as labour, electricity and depreciation are a relatively small part of the cost structure for these producers and there is no sign that this will change in the medium term.
Through the medium term, using CRU’s projections for aluminum and silver prices – and due to the limited potential for substantial falls in polysilicon prices – materials cost increases could offset many of the minor cost reductions we anticipate through improvements in manufacturing processes and reductions in materials usage.
Even when considering cost-per-watt (the typical metric used for PV modules, which takes into account the power and efficiency of a module) we expect only modest declines in manufacturing costs in the next few years.
For the current incumbent technology, PERC (passivated emitter and rear cell), we expect only a small fall even when assuming a static exchange rate. Factoring in the likelihood that the dollar will drop back from its current strong position, PERC manufacturing costs may even increase in ¢/W terms in the mid-term.
Even when considering a newer technology such as TOPCon (tunnel oxide passivated contact), which is set to dominate the industry from 2024 and whereby there are more gains to be made in both processing and cell efficiency, cost reduction will be hard-fought.
What next for manufacturers?
Yet, there are areas manufacturers can look to in order to further drive down costs. Alternative materials is one area. In the latest Solar Technology and Cost report, we explore the outlook for metallization costs, touching on whether substitution of silver with copper could be incoming. Other areas are also ripe for innovation, such as the potential of replacing aluminum frames with galvanized steel, which could drive costs lower but does add slightly to module weight. Widespread substitution here would be highly significant for the pace of demand growth in the aluminum market.
Manufacturers will also continue to look to new technologies to drive up module efficiencies and thereby drive down cost-per-watt. Improved efficiency provides an opportunity to drive down not only module cost-per-watt, but also per-watt costs for many balance of system costs (costs incurred in installing the wider solar system) such as labour, trackers/mounting structures and land.
As detailed in the Solar Technology and Cost Service, the industry is rapidly shifting towards new, higher efficiency, technologies such as TOPCon, heterojunction (HJT) and back contact (xBC) technologies.
To significantly surpass the efficiencies of these technologies, and to drive cost-per-watt even lower, manufacturers will need to look to multi-junction cells. Multi-junction devices involve multiple solar cells stacked on top of each other to better utilise the high-energy portion of the light falling on the device (via the top cell) while still also generating electricity from the lower-energy portion of the light (via the bottom cell).
These designs can enable cell and module efficiencies far above those achievable by single-junction devices. Due to this, and with absolute cost-per-m2 cost reductions now so difficult to achieve for PV manufacturers, we believe they will be highly influential in the longer term.
Yet, a number of key challenges are still to be addressed before this technology can be commercialised. A broad shift towards tandems is not likely until the 2030s, making the task of driving down PV manufacturing costs during the rest of this decade particularly challenging.
The PV market continues to see significant technological innovation, driving uncertainty and risks for module purchasers and for those supplying or investing into the value chain. The magnitude and timing of these technological changes must be thoroughly understood for the creation of accurate industry roadmaps.
Oversupply will pressure prices in the short term
The industry has seen module prices crash in 2023. These falls go beyond simply passing through recent reductions in input costs as polysilicon prices tumbled. All key stages of the industry – from polysilicon to module – are now oversupplied, and high inventory levels in several key markets, such as Europe and the US residential market, have exacerbated this issue.
High levels of imports to the US also point to a building US inventory for modules designed for utility-scale projects, providing another risk for downwards pressures on prices in this important market. Many manufacturers and distributors are now selling inventory below cost, and manufacturers purchasing cells and undertaking only module manufacturing in-house are almost certain to be operating at a loss.
In the near term, prices could continue to decrease as smaller manufacturers, desperate to attain orders, accept financial losses. However, these unsustainable losses cannot continue indefinitely, and it is likely that 2024 will see producers consolidate or curtail capacity. In this environment, any manufacturing cost reductions may feed through to first restoring sustainable margins before enabling any further price reductions. That said, it would require significant consolidation to truly resolve overcapacity through the supply chain.
Monitoring and understanding how these market dynamics are evolving – particularly during what looks set to be a challenging 2024 for manufacturers – is key for all stakeholders, whether buying or selling modules, investing in downstream projects, evaluating investments in upstream manufacturers, or designing policies to regionalise manufacturing and accelerate solar PV deployment.
The CRU | Exawatt Solar Technology and Cost Service will be relaunching in November and will provide data, insight and analysis on solar technology, and cost. Find out more at: Solar Technology and Cost (STAC) Service | CRU (crugroup.com)
Explore this topic with CRU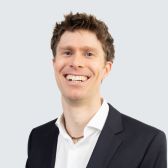
Author Alex Barrows
Head of PV, Exawatt View profileThe Latest from CRU
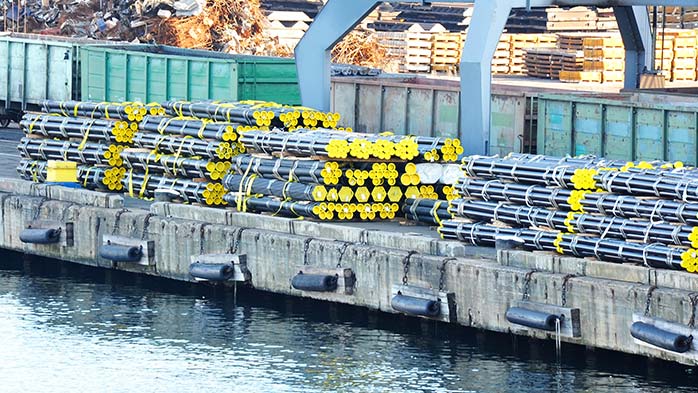
Decarbonisation will reshape global steel trade flow
CRU’s Steel Long Term Market Outlook presents comprehensive analysis of global steel trade flows until 2050. Decarbonisation will play a significant role in redefining...